While nearly every industry uses power drills, screw guns and other standard handheld tooling, some make use of specialized tools, which are often expensive and difficult to supply. Securing these tools from theft and being able to quickly locate them is critical for the manufacturing process. With smart, technology-driven tool-tracking solutions, managing these tools becomes faster and more efficient.
The Technology Kit
The technological enablers of smart tool tracking are radio frequency identification and the Industrial Internet of Things (IIoT). RFID serves as a source of data about tools’ locations, properties and movements, while the IIoT is used for storing, processing and analyzing the data fetched from RFID tags.
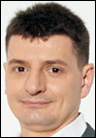
RFID
A typical RFID system includes three components: tags, antennas and readers.
• RFID tags serve as object identifiers. Each tag has a unique ID number that is correlated with information about the object to which a tag is attached, and this data is stored in the cloud. For tool tracking, passive tags are typically used, as they are smaller, cheaper and more mobile. To be able to transmit data, such tags should be supplied with the power from an RFID reader (as opposed to active tags, which do not require power from a reader to be able to transmit data).
• RFID antennas are used to transfer a radio signal to and from readers.
• RFID readers supply the energy for the tags and receive a radio signal back from them. A reader catches radio signals from tags, extracts their IDs, correlates them with the locations of the readers and the time of the reading, and relays the extracted information to the cloud.
The IIoT
The analytics component of the IIoT turns the data fetched from RFID systems into insights about the availability, movements and usage history of each tool. Once analyzed, the data is visualized and displayed to solution users in the form of, say, live tool availability maps.
The Approach
Lightweight asset-tracking solutions based on RFID and IIoT optimize tool tracking from several perspectives. They allow the checking of tool availability and location, as well as the controlling of employee access to specialized assets.
For that, each asset is labeled with an RFID tag, and data regarding each asset is saved to a data warehouse. To enable tool tracking throughout a manufacturing facility (for instance, at tool zone entrances or at the exits), RFID readers are installed to scan the tags. Once a tool passes a reader, the device fetches the tool’s ID and transmits it to the cloud.
The cloud software processes the incoming ID, states the location of the respective tool, and presents the findings to employees via the Web or mobile user applications. If an employee needs a certain tool, he or she can use a mobile app to check that item’s availability and location, then book it.
To prevent unauthorized access to specialized tooling, employees can also wear RFID tags. This way, the reader scans the tags of both the work and the tool. The cloud-based software checks employee record and determines whether he or she is allowed to use that particular tool.
Implementation Examples
Some industry leaders are already using tool-tracking solutions based on RFID and IoT technologies to optimize tool management, control access to specialized tooling and bring down asset-carrying costs. Major industrial adopters of tool-tracking solutions include:
The Automotive Industry
Holt Cat manages tens of thousands of tools used for heavy equipment maintenance and repair. With smart tool-tracking solutions, the company has gained access to real-time data regarding tools’ locations, movements and usage history. The solution paid off in fewer than eight months, allowed the company to optimize tool tracking and promoted tool sharing among more than 15 facilities.
Electronics
Motorola’s Engineering Shared Services electrical lab uses RFID to monitor costly equipment worth more than $3 million in total (including oscilloscopes, function generators, calipers, power supply units, etc.). Along with location tracking, the company applies smart tracking technologies to control employee access to the tool zone.
Construction
Grunnarbeid, a Norwegian construction company, uses a smart asset-tracking system to track tools as they move at and between construction sites and a central equipment warehouse. The company keeps track of more than 1,000 high-value handheld tools. Using a smart tool-tracking system, the enterprise managed to reduce tool delivery costs by $4.3 million.
Benefits
Tool-tracking systems based on RFID and the IIoT drive both process and business improvements, including:
Increased Tool Accountability and Traceability
Handheld tools can be lost, misplaced and stashed by workers. Smart tool-tracking solutions help to prevent these issues by providing asset specialists with real-time data into the location, movements and usage history of each tool.
Reduced Tool Search Time
Technicians spend a lot of time searching for tools, which may not be at hand when required. This can lead to a decrease in productivity and job satisfaction, as well as missed production deadlines. With smart tool tracking, workers can easily access real-time data about tool location, so they waste no time searching for the required tooling.
Increased Tool Sharing
Tool-tracking systems based on RFID and the IIoT provide a real-time view into a tool’s availability. Given this data, several employees can schedule tool usage, which frees an enterprise from the need to buy additional tooling.
Theft Prevention
According to a recent survey carried out by Volkswagen, during the past three years, tool thefts have costed businesses an estimated $60 billion. Tool-tracking solutions help to identify and prevent equipment theft by detecting when a tool leaves a manufacturing facility or a warehouse.
Limitations
Before implementing an RFID-enabled tool-tracking solution, businesses need to consider the following points:
• RFID tags should not influence the production process, complicate the work of employees, threaten their safety or intervene with a tool’s performance. To ensure that, the selection of tags should be based on a particular read range, a specific tag size and compliance standards. In addition, the placement of the tags should be carried out under simple, comprehensive guidelines.
• The cost of tools should be high enough for a tool-tracking system to pay off. The price for RFID tags ranges from 5 cents to $10 per item, while the price of a reader can be as high as $5,000 to $20,000, which doesn’t make RFID a good fit for tracking, say, screwdrivers. However, an RFID-driven solution is sure to pay off when applied for tracking costly tooling.
To Sum Up
In the industrial ecosystem, a missing tool can do more harm to the production schedule than a missing part. Inefficient to be tracked via traditional methods (say, spreadsheet-based), tools’ locations, movements and usage history can be effectively monitored with RFID and IIoT technologies.
By providing technicians and asset specialists with real-time updates about each tagged tool, smart tool-tracking solutions can help industrial enterprises to reduce tool search times, optimize tool usage and bring down inventory-carrying costs due to increased tool traceability, availability and sharing.
Boris Shiklo, ScienceSoft‘s CTO, is responsible for the company’s long-term technological vision and innovation strategies. Under his supervision, the company’s development team has successfully fulfilled complex projects of more than 80,000 man-hours in health care, banking and finance, retail, telecommunications, the public sector and other domains. Boris has a solid background in IT consulting, software development, project management and strategic planning.