Nedschroef, a Dutch producer of metal fasteners for the automotive industry, has reduced the incidence of shipping errors at its plant in Plettenberg, Germany, down to 1 percent using radio frequency identification technology.
The company is employing the solution to manage 4,500 square metal containers, each filled with as many as 100,000 nuts. While awaiting shipping, the containers are stored within an automated rack. By affixing an RFID tag to each container (as well as mounting a second tag to a production sheet attached to that container), Nedschroef can track production information and the containers’ exact weights, in order to ensure that the proper number of fasteners are shipped to each customer.

Nedschroef needs to know each container’s empty weight—which can vary by as much as 2 kilograms (4.4 pounds)—because it must calculate the exact weight of every container’s contents before the nuts are repacked and shipped to customers. Before an empty container is filled, Nedschroef weighs it and then utilizes a Nordic ID Merlin handheld RFID device to write the tare weight data to a Confidex SteelWING RFID tag attached to the framework supporting the container’s leg.
Klaus Menken, Nedschroef’s project manager at B&M Tricon—the Vienna-based designer and integrator for the application—says Nedschroef chose the Confidex tag because it is flexible and is not typically damaged by coming into contact with a forklift. In addition, he notes, the tag is small and fits well on the containers.
To track production information, workers use the plant’s enterprise resource planning (ERP) system to print a production order on a piece of A4 paper, using an Avery Dennison AD 224 RFID tag glued to the back. The production order and tag are printed and encoded simultaneously via one of three Lexmark T642 printers. Information regarding the type of nuts, along with their individual item weight, is stored on the RFID tag, after which workers place the RFID-enabled production sheet into a plastic sleeve that is then attached to the metal container’s side.
As the full container is being weighed in the loading station, an Intermec IF61 ultrahigh-frequency (UHF) reader equipped with two different antennas reads both RFID tags . The system collects the tare weight and the production order information from the tags, forwards that information, along with the full container’s weight, to the ERP and warehouse-management systems, and then calculates how many nuts are in the container.
In the event that an error is detected—for instance, if a tag cannot be read, or if the container is deemed too heavy—the automated rack system moves the container to the side on a belt, where an employee can then investigate the problem. Once all data has been collected and calculated, and after an approval for storage has been received from the automated rack system, the containers are automatically moved and stored, to await shipment. The company’s picking and shipping processes currently do not utilize RFID.
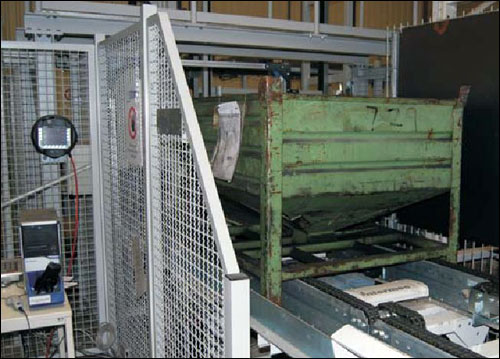
Nedschroef chose to employ two separate tags—with one tag (for tracking weight information) attached to the container, and the other (for tracking production information) affixed to the printed production order—”because it is never clear which container will be used to store which nuts,” says Joachim Reuter, a Nedschroef employee in charge of IT.
One main benefit provided by the system, Reuter says, is the ability to know and track an almost precise number of nuts that Nedschroef produces and sells. The Plettenberg plant alone manufactures 4,000 different types of nuts, and each container can hold up to 100,000 pieces, weighing a total of 800 kilograms (1,764 pounds).
“We have an error rate of only 1 percent with such a huge number of nuts,” Reuter states.
According to Reuter, the company has saved significantly since deploying the RFID system, since it can now more precisely calculate the number of nuts that it produces and sells. What’s more, containers no longer end up misplaced or lost, and since workers need not spend their time searching for containers, Nedschroef also saves labor costs. He declines, however, to provide specific figures.
B&M Tricon reports that, thanks to the space between the plastic sleeve for the production sheet and the metal container, the system has no trouble reading the RFID tag inside the sleeve. Nedschroef uses approximately 90,000 of the Avery Dennison tags annually.
Nedschroef installed the solution at the beginning of 2008. Moving forward, Reuter says, the firm is considering installing readers in order to track each order’s production status.
According to Menken, Nedschroef is looking to install up to 14 forklift readers that would interrogate the tag of each container as it is moved around the facility. Nedschroef would be able to know which production steps had been completed, depending on the forklift’s location—for example, if the vehicle left a hall carrying a container, the system would deduce that the production step was completed. Operators would roughly estimate the forklifts’ locations within the facility, Menken explains, via a signal-strength comparison of signals transmitted by the forklift readers at designated points within the plant.
The advantage of placing interrogators on the forklifts, Menken says, is that additional reader infrastructure would not be required along the production line. What’s more, he adds, inbound containers being returned by third-party partners could be identified as they were offloaded from trucks.