Editor’s note: As we get toward the end of 2023, RFIDJournal.com is looking back at some of the top stories that we published in the last year.
The hospitality industry is collectively one of the largest users of linens and linen garments throughout the world, with ownership of billions of sheets, towels and robes, as well as staff uniforms. These flat, uniform-based linens are an essential part of the operations and services at hotels, casinos and theme parks, as well as aboard cruise ships.
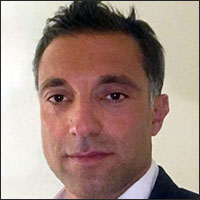
Fabrice Morini
Many companies track and manage these high-value, large-volume items via technology, while others operate a manual system of identifying and monitoring goods as they are used, laundered and then returned to guests or employees. But regardless of how asset management might be accomplished, the use and oversight of linens requires a lot of resources, including operational, financial and environmental, to identify the technology’s value. There are steps companies can take to make sure such a system is used properly.
RFID Journal discussed this topic recently with Fabrice Morini, the worldwide sales director of HID Global‘s Textile Services Business Unit. Morini says several issues are driving a movement toward radio frequency identification (RFID) technology to track linen assets. Those include the high cost of labor at hotels and resorts, as well as rising expenses related to stock loss or shrinkage. The latter concern is especially felt at high-end facilities, he notes, where branded terry-cloth toweling tends to disappear in great numbers. In fact, losses represent approximately 15 to 20 percent of hotels’ linen costs.
RFID’s Benefits for Linen Management
The primary benefit of RFID is the automatic identification of every item, from a face cloth or towel to an employee’s jacket or trousers. With passive HF or UHF tags applied to assets, along with readers deployed at specific chokepoints in the laundering and management processes, companies can gain a real-time view into each item’s status. The tags can be read not only as goods enter or leave a laundry area, but also at spas, pools or beaches, where theft poses the greatest risk.
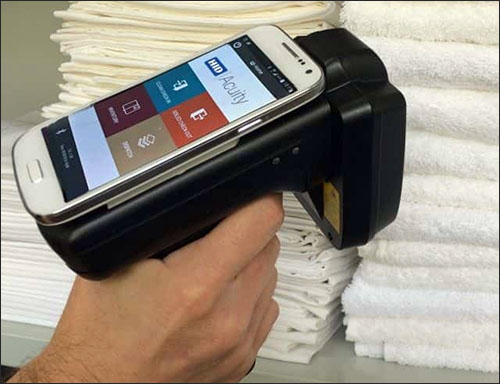
An RFID linen-tracking system from HID
There are several business models for linen management. The majority of large hospitality companies outside of Europe own and manage their own assets within their hotel or resort facilities. Most companies in Europe, however, rent their linens from a third-party provider that also supplies laundry services.
“We have noticed that more and more high-end hotels [have] moved away from laundry rental services,” Morini explains, “and [have] chose[n] to own their linen and terry textiles.”
When it comes to employee uniforms, casinos, hotels and cruise lines typically opt for a solution that records and tracks who is responsible for each outfit, then monitors inventory levels and monitors each garment’s current location, such as “checked out by an employee” or “in the laundry process.” RFID solutions typically involve either a 13.56 MHz HF RFID tag compliant with ISO 15693, or a UHF tag with a relatively longer read range. These washable tags can be sewn into or heat-sealed to each asset, and then encoded with a unique ID number that is managed in the company’s own software, or in the cloud by a third party.
The RFID readers capture those tag IDs as the assets move through their cycles. “With our RFID-based linen-management platform,” Morini says of HID’s software and RFID tags and hardware, “they can better control their stocks, turnaround times and linen quality.”
Most often, he says, customers come with straightforward requests, including “Can you help me identify my pain points?” and “Can you provide a rough timeline, to be used to synchronize with the linen availability?” and “What are the KPI’s [key performance indicators] that will measure the RFID implementation’s savings and benefits?”
Evaluating the Site and Demands
Following some simple steps can help companies ensure that they have deployed an RFID system in a way that provides those KPIs. The first things a business needs to do, Morini explains, is to evaluate its facility’s space and operations on site, as well as select an RFID linen-management expert to assist. The expert should be expected to conduct both an environmental and operational analysis to define the specifications.
By understanding the flow of linens, both guest-side flat linens and employee-facing uniforms, a team can decide where and how many RFID reading stations need to be deployed. In some cases, RFID tunnel readers are installed where assets are conveyed into and out of laundry areas, while fixed readers can be used on laundry chutes, as well as in portals through which carts of linens are transported.
Handheld readers enable staff members to conduct inventory counts in linen rooms or searches of specific items.
Developing a Tagging Plan
Once the reader infrastructure has been mapped out, companies need to focus on how to uniquely identify each asset. This can be a complex process that often requires the tagging of new and existing assets in high volumes. Most linen companies provide RFID tagging for their products at the point of manufacture, making the process easier for end users.
In other cases, a company may need to apply tags to their existing and new assets. An RFID technology provider should offer integration guidelines not only for fixing different types of RFID tags onto different types of textile items, but also for integrating the RFID tag data with the company’s existing management software.
To bring RFID tags into a company’s processes, RFID-enabled items need to be encoded following the user’s product reference list as they will be viewed and identified in the system. From that point forward, every tag read will update the product’s status in the management software.
Power and Network Requirements
By the time a company reaches the next step, early planning should have helped the company to identify the technical prerequisites at its site. That includes the laundry or hotel’s network and power supply at the points at which tags need to be read. Each RFID reader will require a power source, as well as server access, which could be accomplished via Ethernet cables, or using Power-over-Ethernet (PoE) with standalone readers to reduce cabling requirements.
Before taking an RFID system fully live, resorts, hotels or other users should conduct onsite testing, as well as ensure that personnel receive the necessary training. In addition, users will want to be sure the software being used provides relevant data, including accessible dashboards for real-time views into where linens are located, sorting by category, and status indication. The system should provide reports to identify trends according to dates, sites and product categories, as well as utilization rates over time.
Benefits to Expect
If the solution is properly deployed and leveraged, it should provide numerous benefits. Preventing the loss of goods can be accomplished by identifying the point at which the assets go missing and then addressing those issues. Those using HID’s Textiles solution have reported a loss reduction of 50 percent, according to the company.
What’s more, customers have reported a reduction in labor costs of up to 30 percent, thanks to the digitalization of linen- or garment-management process. This can be accomplished by reducing the need for manual inventory counts, sorting, check-ins and check-outs of goods moving through laundering or repairs processes.
Thanks to the shrinkage reduction, Morini says, companies are seeing a drop in purchasing by up to 20 percent annually. The visibility automation makes redundant purchases unnecessary, since companies know where their assets are, whether they are in a linen room, a guest room or a laundry area, or if they are in transit.
When used to capacity, the technology can help businesses ensure linen quality control. Users know how each asset has been utilized, along with the exact number of wash cycles per item, and they can remove weathered or damaged items from the supplies. Long-term analysis, meanwhile, can help a company ensure that its assets are used according to their life-span, and understand how well specific products hold up over time.
Key Takeaways:
- A four-step strategy can help resorts, hotels and other hospitality companies deploy the right RFID solution.
- Once a UHF RFID system is in place, businesses can achieve gains based on the improved visibility of each textile asset used in running the business and serving guests.