Technology startup Compike has developed a social-distance tracker for COVID-19 infection management that keeps data private from employers unless a positive test is reported. The solution is aimed at fighting the global coronavirus pandemic in office or workplace environments without requiring technology infrastructure. The system consists of 2.4 GHz trackers that send and receive transmissions to detect contacts within a distance of 2 meters (6.6 feet), then store that content without transmitting it to a server.
The device, worn by each worker, collects data regarding the individuals with whom it has been in contact. It sounds an acoustic and visual alarm in the event of a critical contact, and it enables the downloading of data to a server for positive test results. Compike’s software can then trace all contacts for that device for the previous 14 days.
The Heidelberg-based company was launched by Patrick Hartmann, Compike’s CEO, who was previously the chief sales officer at Kathrein Solutions and the global sales director at noFilis Auto ID (which Kathrein acquired in 2016). He launched Compike in May 2020 to address the need for automatic-identification solutions capable of locating assets, as well as tracking inventory or the movements of personnel in various industries. The firm is focused on custom solutions for a variety of applications using multiple technologies, including RFID and other Internet of Things (IoT) systems.
“We know the market [and] we know the available technologies,” Hartmann says, including RFID, real-time location systems (RTLS), Bluetooth Low Energy (BLE), LoRa or mixed hybrid solutions. “One of the key differentiators is that we are flexible in selecting the best technologies for a specific use case.” In the long term, Compike plans to provide auto-ID solutions for government businesses and private entities. It also provides generic tracking and tracing functionality for smart traffic solutions and smart seals for freight vehicles.
However, Hartmann says, when the coronavirus sent workers home in Germany and worldwide, all business plans changed. “We thought, ‘Hey, what can we do to potentially contribute to solving the COVID situation, especially as the lock downs are lifted?'” Considering the company’s technical expertise, he says, “We decided to develop and promote this social-distancing solution” to address COVID-19 back-to-work challenges. While the company is currently in discussions with several potential customers for other auto-ID solutions, the initial focus is the COVID-19 solution.
Hartmann’s previous company has already sold more than 100,000 wireless track-and-trace units for use in construction and building machines, in order to track their movements, and those same devices have now been reconfigured for tracking individuals. “That’s how we were able to bring this solution to the market so quickly,” Hartmann explains.
Regarding the existing contact-tracing and social-distancing solutions being released, Hartmann says, the company wanted to offer a simpler solution that would not require readers or gateways. Instead, he adds, Compike designed the tracker units for the lowest possible rollout complexity. The company opted for active RFID transmissions to be both sent and received by the trackers, without the need for fixed readers.
Businesses can opt to deploy readers if they want access to the data or specific location information. The 2.4 GHz RFID transmissions will not interfere with existing Wi-Fi or Bluetooth systems, Hartmann says. Once a company purchases the solution, he explains, “They unpack it, start the software tool, associate a tracker to a person by typing them [into the cloud-base software] manually or scanning a barcode, and they are ready to go.”
The tracker is designed by Compike and manufactured by a third-party manufacturer according to that design. The battery-powered device comes with a multi-colored LED light. The unit can be worn on a lanyard or belt clip. Its built-in 2.4 GHz radio transmits at preset intervals, and the device’s data can be password-protected. Each time the tracker comes within range of another tracker—approximately 2 meters (6.6 feet)—the transmission is sent and received by both devices. Each responds by emitting an acoustic alert and flashing red. The individuals can then step away from each other to maintain a safer distance.
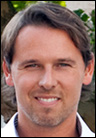
Patrick Hartmann
Each tracker measures how long it remains within range of another device, and that data is saved on its internal flash memory. The unit can be recharged every few weeks, and it automatically erases data that is more than two or three weeks old, depending on an employer’s needs.
If an individual tests positive for COVID-19, he or she would report to management and turn in his or her tracker. Using a password, an official from human resources, the local health department or coronavirus taskforce can download the tracker’s contacts record from the prior 14 days. Those critical contacts can be viewed, and officials can reach out to each individual and suggest she or he get tested or quarantine themselves. Data privacy is central, Hartmann adds; those who do not test positive need not share their contact history, so the system is less invasive for workers.
The tracker’s rechargeable battery life varies, depending on how often it beacons. If it transmits every 20 seconds, for example, the battery can last for about 14 days. However, companies can configure for other transmission frequencies, such as every 10 seconds or every five minutes. Each device can store data from up to 1,000 trackers. “Momentum has been great,” Hartmann says, adding that the company is shipping units and providing implementations. The businesses using the technology have asked not to be named. However, he says, these customers are generally in the logistics, manufacturing and tourism sectors.
For instance, a cruise ship could provide tracker units for each of its guests as they arrive on board, as well as for employees. The unique ID number on each tracker would be linked to the corresponding individual in the cloud-based Compike software. The could benefit from having more precise information regarding the historical interactions of any guests or employees who have tested positive for COVID-19. Thus, rather than having to test an entire cruise ship in the event of a positive test result, a company can identify and isolate anyone who may have come in contact with an infected individual.
The company is currently seeking partners that sell the units as part of a solution. “We have resellers around the globe,” Hartmann states. To date, he says, the product has had a presence in the Middle East, the United States, Asia and the European Union. He predicts the solution will be in demand for the next 12 to 18 months, after which companies will be able to contact Compike or their partners to learn how the trackers could be used for other purposes, such as logistics, warehouse management, work-in-progress tracking, security or vehicle management.